Vibration Testing Fixtures
Paragon Systems is unique in being able to not only perform your vibration test, but also to design, fabricate and qualify your vibration testing fixtures. Usually all we need from a client is their vibration test profile, a CAD model and the GD&T of the DUT.
With this information, our in-house fixture design team will produce an initial design, optimize it with FEA, fabricate it, qualify its resonance performance and measure its dimensional accuracy-all in-house. vibration testing fixtures
This one stop service allows us to control both cost and schedule better than a provider who outsources vibration fixture design and fabrication or a provider who relies the client to design and fabricate the fixture themselves.
Our experience as a vibration testing fixture manufacturer ranges from small solid cube fixtures, head expanders and to large complex structures weighing as much as 450 kg.
Each vibration testing fixture we deliver includes a qualification report describing the dynamic response characteristics for each product mounting location and if the client requires, we can also furnish a dimensional inspection report. vibration testing fixtures
Vibration Test Fixture Basics
Interface:
A vibration testing fixture provides the interface between the shaker test surface and the device under test (DUT). In a perfect world, the mounting points for the DUT on the fixture would exhibit the same mechanical impedance and dimensional characteristics of the mounting surfaces that are used in the actual application.
In the real world, the mechanical impedance goal is extremely difficult to achieve in a cost-effective matter. Because of this, what we try to do in a vibration test fixture design is to produce a fixture which transmits the mechanical energy from the shaker into the DUT on 1:1 basis (i.e. maintaining the specified tolerance for the vibration profile) throughout the test frequency range. – vibration testing fixtures
The practical outcome of this approach in a real-world vibration test fixture, is an absence of fixture resonances in the test frequency range.
Stiffness:
Achieving resonance free performance requires a vibration test fixture to be extremely rigid. Fixtures should be stiff enough and be significantly stronger than the specimen to transmit the energy into the DUT without fatiguing.
When a fixture exhibits resonances, the energy transmitted into the DUT is increased. This increase in energy can easily exceed the tolerances for the vibration test profile and in extreme cases be as high as 10 to 30 times higher than the nominal test level. DUTs which are tested on fixtures which exhibits resonances can be over-tested in the frequency ranges where the resonances occur. vibration testing fixtures
Resonances are not the only negative outcome we are trying to avoid in a good vibration fixture. In addition to exhibiting resonances, a fixture can also exhibit frequency ranges where vibration energy is being damped. In these regions, the vibration energy can be reduced nearly to zero and result in a DUT which is under-tested within the frequency ranges.
Mass:
Mass is an important consideration in vibration test fixture design because shakers don’t have an unlimited capacity to move objects. One of the design objectives of vibration fixture is controlling the weight of the total package being tested.
One of the reasons to control total mass is when testing a DUT which itself exhibits resonance. DUTs that exhibit high ‘Q’ resonances require shaker amplifier power to control those resonances to bring the vibration energy within the test tolerance.
Even though a DUT might not be heavy enough to strain the force limit of a shaker, it’s important that we limit a total mass that needs to be moved by the shaker.
Occasionally a vibration test fixture can’t be designed which is completely free of resonances, either because it is too large or the test frequency range is very high or both. In these cases, the fixture will resonate. A heavier fixture with high ‘Q’ resonances requires shaker amplifier power to control.
Material Selection:
Vibration fixtures can be made from many different materials, but aluminum and magnesium are the most commonly used. Each has its advantages, with aluminum obviously being more economical than magnesium. While magnesium is lighter than aluminum, it also has other advantages over aluminum when resonances are unavoidable in a fixture design.
Fabrication:
Smaller fixtures can be machined out of solid blocks of material. This is usually not practical for larger fixtures. Larger fixtures tend to be assembles of separate components which are brought together and connected to provide the necessary rigidity.
Dimensional Accuracy:
Earlier we described the mechanical impedance and dimensional characteristics of an ideal vibration test fixture. While mechanical impedance of actual DUT installation is difficult to achieve, dimensional accuracy should not be. It’s important for a vibration text fixture to be dimensionally accurate, so that when a DUT is mounted to the fixture, the mechanical stress imposed on the DUT is the same as the mounting stress it experiences in the actual installation. vibration testing fixtures
More From Paragon Systems
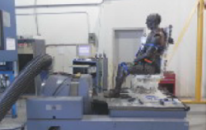
Vibration Testing Services
Vibration testing can be applied using either sine, random, sine-on-random or narrow band …
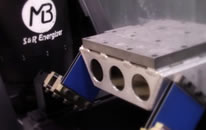
BSR Testing
Annoying vehicle noises in vehicle interiors occur when incompatible contacting material pairs move in relation to each other.

Mechanical Shock Testing
The electrodynamic vibration test machines are also used to generate highly repeatable mechanical shock …
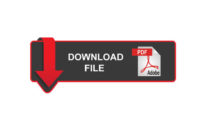
Case Study
Controlling Fixture Resonances
Resonances are great for musical instruments, but except for some …